Utilisation du régulateur PID AI-518P de XIQI Electronic&Technology pour le brassage
Introduction
Cet essai fait suite à l'essai relativement réussi du régulateur CR 20 de Canard Rouge. Le but étant maintenant d'aller jusqu'à pouvoir programmer une séquence de brassage complète dans le régulateur. J'ai cherché pas mal de temps pour trouver un produit à un prix abordable pour un brasseur amateur et qui pourrait assurer ces fonctions.
Le régulateur CG AI-518P deXIQI Electronic&Technology est un régulateur à intelligence artificielle qui accepte un programme à 30 pas de programme. Son coût est relativement modéré pour un appareil de ce type (autour de 60 € frais de port compris)
Grâce à son nombre important de pas de programme et à sa fonction multi-courbes, nous pouvons y mémoriser plusieurs programmes de brassage (leur nombre dépendant du nombre d'étapes de ces programmes).
Il est utilisé ici pour piloter un relais statique SSR par modulation d'impulsions temporelles.
On se reportera à l'article Modification du Robobrew V2 pour régulation par PID et contrôle de la puissance d'ébullition pour savoir comment équiper le Robobrew d'un relais statique. Son installation sur d'autres appareils de brassage ne devrait pas être très différente.
Notice de fonctionnement de l'appareil
Avertissement : cette traduction a été réalisée dans le but d’apporter une aide aux utilisateurs francophones. Partant d’une traduction (probablement du chinois vers l’anglais par une personne dont ce n’est apparemment pas la langue maternelle) bien que le plus grand soin lui ait été apporté, cette traduction risque de cumuler les erreurs ou imprécisions des deux traducteurs. C’est pourquoi, le traducteur décline toute responsabilité sur les événements et effets dommageables qui pourraient résulter de l’utilisation de cette traduction. En cas de doute ou de danger possible sur tel ou tel point, l’utilisateur est appelé à consulter les services techniques du fabricant.
Voir la version en pdfLa notice étant relativement longue, pour faciliter la lecture de la page, je l'ai divisé en 3 parties repliables. Chacune des parties peut être affichée en cliquant sur le lien [afficher] à l'extrême droite.
NOTICE : PREMIÈRE PARTIE — EN BREF (afficher ☛)
1. EN BREF
1.1. Fonctionnalités principales
• Utilise la technologie de calibration numérique pour les entrées de mesure avec une précision de 0,25 % de la pleine échelle (F.S.0.25%).
• Utilise un algorithme avancé d’intelligence artificielle, pas de dépassement avec la fonction d’auto-ajustement (AT auto-tuning) et l’auto-adaptation.
• Utilise une organisation avancée modulaire, fournissant de manière aisée une foultitude d’options en mesure de satisfaire des applications variées, faciliter une livraison rapide et la maintenance de l’instrument.
• Une interface personnalisable autorisant une utilisation facile et rapide. Les paramètres peuvent être promus pour un accès immédiat par l’opérateur dans la table des paramètres de champ ou protégés par un mot de passe dans la table complète des paramètres.
• Doté d’une alimentation universelle 100-240VAC ou 24VDC et de dimensions variées au choix de l’utilisateur.
• Certifié ISO9001 et CE, atteignant un niveau de qualité de classe mondiale, une protection contre les parasites et la sécurité.
POINTS APPELLANT VOTRE ATTENTION
Ce manuel est pour la version 8.1 du CONTRÔLEUR INDUSTRIEL À INTELLIGENCE ARTIFICIELLE AI-518/AI-518P.
Certaines fonctions évoquées dans ce manuel ne s’appliquent probablement pas à d’autres versions de l’instrument.
À la mise sous tension de l’instrument, le modèle et la version logicielle s’affichent. L’utilisateur est invité à porter une attention soutenue aux différences entre les versions lors de l’utilisation de l’instrument. Merci de lire ce manuel attentivement afin d’utiliser l’instrument correctement et d’en tirer le maximum.
Veuillez définir les paramètres en accord avec les types et fonctions d’entrée/sortie.
1.2. Définition du code de commande
Une conception matérielle modulaire avancée est utilisée pour les instruments des séries AI. Il y a au maximum cinq emplacements de modules : entrée/sortie multi-fonctions (MIO), sortie principale (OUTP), alarme (ALM), sortie auxiliaire (AUX) et communication (COMM). Les modules peuvent être achetés ensemble ou individuellement et assemblés librement. Le type d’entrée doit être défini comme thermocouple, RTD ou courant/tension linéaire.
Le code de commande des instruments des séries AI-518/AI-518P (V8.1) comprend 9 parties. Par exemple :
Cet exemple montre que :
• le modèle de l’instrument est AI-518,
• les dimensions du panneau avant sont 96x96 mm,
• aucun module n’est installé dans l’emplacement MIO,
• un module de sortie en courant linéaire X3 est installé dans l’emplacement OUTP (sortie principale),
• un module à deux relais électro-mécaniques L3 est installé dans l’emplacement ALM (alarme),
• aucun module n’est installé dans AUX (sortie auxiliaire),
• un module S4 (module de communication RS485 ) est installé dans COMM,
• la tension d’alimentation est 24VDC,
• une entrée étendue du type (pyromètre à radiations F2) est disponible.
Voici la description détaillée des 9 parties :
① Indique le modèle de l’instrument
• AI-518 type économique de l’instrument d’une précision de 0,25 % de la pleine échelle (F.S.0.25%). Il met en œuvre la technologie de contrôle par intelligence artificielle, dispose des fonctions de contrôle, alarme, retransmission et communication.
• AI-518P Basé sur AI-518, y ajoute 30 pas de programme.
② Précise les dimensions du panneau avant (largeur×hauteur)③ Précise le type du module d’entrée/sortie multi-fonctions (MIO). Les modules possibles sont I2, I4, K3, V, etc. N signifie qu’aucun module n’est installé.A (A2) 96×96 mm . La découpe fait 92×92 mm. La profondeur derrière la surface de montage est de 100 mm.
B 160×80 mm. La découpe fait 152×76 mm. La profondeur derrière la surface de montage est de 100 mm.
C(C3) 80×160 mm. La découpe fait 76×152 mm. La profondeur derrière la surface de montage est de 100 mm.
D 72×72 mm. La découpe fait 68×68 mm. La profondeur derrière la surface de montage est de 95 mm.
D2 48×48 mm. La découpe fait 45×45 mm. La profondeur derrière la surface de montage est de 95 mm.
E 48×96 mm. La découpe fait 45×92 mm. La profondeur derrière la surface de montage est de 100 mm.
F 96×48 mm. La découpe fait 92×45 mm. La profondeur derrière la surface de montage est de 100 mm.
D5 Montage sur rail 22,5×100×112 mm (largeur×hauteur×profondeur). Installé sur un rail DN et programmé depuis un terminal externe E8.
E5 Montage sur rail 48×96×112 mm (largeur×hauteur×profondeur). Installé sur un rail DN et programmé depuis un terminal externe E8.
④ Précise le type de module de la sortie principale (OUTP). Les modules possibles sont L1, L2, W1, W2, G, K1, K3, K5, K6, X3, X5, etc.
⑤ Précise le type de module d’alarme (ALM). Les modules possibles sont L0, L2, L4, L3, W1, W2, G, etc.
⑥ Précise le type de module de sortie auxiliaire (AUX). Les modules possibles sont L0, L1, L2, L4, L3, W1, W2, G, K1, X3, X5, etc.
⑦ Précise le type de module de communication (COMM). Les modules possibles sont S, S4, V etc.
⑧ Précise l’alimentation de l’instrument. Si cette partie est laissée en blanc, l’alimentation est 100~240VAC. Si 24VDC est précisé, alors l’alimentation est 20~30V DC ou AC.
⑨ Précise une extension de spécification optionnelle (si absente laisser en blanc). La série d’instruments AI-518 prend en charge de nombreux types d’entrée dont les populaires thermocouples, RTDs, tension linéaire, en courant et résistantes. Si besoin, une spécification non mentionnée dans la table de sélection de type (InP) peut être ajoutée.
Note 1 : l’instrument met en œuvre la technologie du zéro automatique et de la calibration numérique. Il est sans maintenance. Si l’erreur excède une certaine plage, en général, un nettoyage et un séchage de l’instrument peut y remédier. Si ce n’est pas le cas, renvoyez l’instrument à l’usine pour examen et réparation.
1.3. Modules
1.3.1 Emplacements de module
Les séries d’instruments AI-518P disposent de cinq emplacements d’installation de module (les instruments de taille D disposent seulement de 3 emplacements OUTP , AUX et COMM/AL1 ; les instruments de taille D2 n’en ont que 2 : OUTP et COMM/AUX). En installant les modules ad hoc, le contrôleur peut répondre aux exigences des différentes fonctionnalités et types de sortie.
Entrée / sortie multi-fonctions (MIO)
Peut recevoir le signal de deux transmetteurs câblés ou un signal 4-20 mA en installant un module d’entrée de courant I4. Le module I4 peut fournir le 24 VDC aux transmetteurs. Si un module I2 (entrée on-off), l’instrument est en mesure de commuter les consignes SV1 et SV2 sur ordre transmis par un contact extérieur. En coopération avec OUTP et en installant un module K3 on peut en faire une sortie triphasée de déclenchement de thyristor à déclenchement et extinction au passage par zéro du courant.
Sortie principale (OUTP)
Ordinairement utilisée comme sortie de contrôle telle que contrôle marche/arrêt, contrôle PID et AI PID. Elle peut être utilisée comme une sortie de retransmission de la valeur mesurée du procédé (PV) ou de la consigne (SV). En installant un module L1 ou L4 on peut la transformer en une sortie par relais électromécaniques ; en installant un module X3 ou X5, en une sortie courant linéaire 0-20 mA ou 4-20 mA ; en installant un module G en une sortie en tension pour piloter un SSR ; en installant un module W1 ou W2 en une sortie sans contact par TRIAC.
Alarme (ALM)
Ordinairement utilisé comme sortie d’alarme. Prend en charge une sortie relais à contact normalement ouvert + normalement fermé (AL1) en installant un module L0 ou L2, ou deux sorties à contact normalement ouvert (AL1+AL2) en installant un module L3.
Sortie auxiliaire (AUX)
Dans un système à sorties duales chauffage / réfrigération, un des modules X3, X5, L1, L4, G, W1, W2 peut être installé pour disposer d’une deuxième sortie de contrôle. Elle peut aussi servir de sortie d’alarme en installant un des modules L0, L2 ou L3 ou être utilisée pour communiquer avec un ordinateur à l’aide d’un module R (interface RS232).
Interface de communication (COMM)
Un module S ou S4 peut y être installé pour communiquer avec un ordinateur (via une interface RS485) Un module de sortie de tension peut aussi y être installé pour servir d’alimentation à un capteur extérieur.
1.3.2 Modules couramment utilisés
N Pas de module installé (ou nul)
L0 Module de sortie par relais électromécanique (courant nominal 2A/250VAC, normalement ouvert/normalement fermé
L1/L2 Module de sortie par relais électromécanique (petit volume, normalement ouvert + normalement fermé, courant nominal 1A/30VDC, 1A/250VAC adaptés aux alarmes, le module L1 passe 2A en nominal).
L4 Module de sortie par relais électromécanique (contact normalement ouvert, courant nominal 2A/30VDC, 2A/250VAC)
L3 Module de sortie double à relais électromécaniques (contact normalement ouvert, courant nominal 2A/30VDC, 2A/250VAC)
W1/W2 Module de sortie discrète par TRIAC pas de contact mécanique, normalement ouvert pour W1, fermé pour W2 (courant nominal 0,2A/100-240VAC)
G Module de sortie en tension pour piloter un relais statique SSR (DC 12V/30mA)
G5 Équivalent à deux modules G
K1 Module de sortie pour déclenchement de thyristor à déclenchement et extinction au passage par zéro du courant en monophasé (peut déclencher un circuit de TRIAC ou une paire de SCR montés tête bêche pour des courants de 5 à 500A)
K3 Module de sortie pour déclenchement de thyristor à déclenchement et extinction au passage par zéro du courant en triphasé (peut déclencher un circuit triphasé, chaque circuit peut déclencher un TRIAC ou une paire de SRC montés tête bêche pour des courants de 5 à 500A), seulement en 50 Hz.
K5/K6 Module de sortie de déclenchement de thyristor en décalage de phase en monophasé 220VAC/380VAC (peut déclencher un circuit de TRIAC ou une paire de SRC montés tête bêche pour des courants de 5 à 500A), seulement en 50 Hz.
X3/X5 Module de sortie en courant linéaire (sortie courant continu 0-22 mA, sélectionnable dans la plage 0-10 mA, 4-20 mA, etc.). X5 est doté d’une alimentation opto-isolée.
S/S4 Module doté d’une interface de communication RS485. S4 dispose d’une alimentation opto-isolée.
R Module doté d’une interface de communication RS232.
I2 Module doté d’une interface d’entrée pour recevoir un contact de commutation ou un signal de fréquence. Dispose d’une alimentation 12VDC pour alimenter un transducteur externe.
I4 Module d’entrée analogique 4-20 mA/0-20 mA. Dispose d’une alimentation 24VDC/24 mA pour alimenter un transducteur.
V24/V12/V10/U5 Module de sortie de tension isolée 24V/12V/10V/5V DC avec un courant maximum de 50 mA. Peut alimenter un transmetteur.
1.3.3 Installation et remplacement de modules
Avant la livraison de l’instrument, l’installation des modules est faite sur demande, et les paramètres sont définis en conséquence. L’utilisateur peut remplacer ou installer des modules par lui-même si besoin est. Lors du remplacement d’un module, vous devez tirer le contrôleur en dehors du boîtier d’abord. Glisser un petit tournevis plat entre le module d’origine et le connecteur sur la carte mère pour retirer l’ancien module et en installer un nouveau. Le changement de module nécessite une modification des paramètres le concernant.
1.3.4 Isolation électrique des modules
Il y a une alimentation 24V et une alimentation 12V pré-existantes dans l’instrument qui sont isolées du circuit principal. L’alimentation 24V alimentent ordinairement les modules de sortie en tension tels que V24/V12/V10/V5, I2 et I4. L’alimentation 12V ordinairement alimente les sorties ou le module de communication. Généralement , les sorties à relais électro-mécaniques et sortie discrète à TRIAC sont auto-isolée des autres circuits, peu importe que d’autres modules soient installés ou pas. La sortie tension pour pilotage de SSR n’a pas besoin d’être isolée des circuits d’entrée parce que les SSR disposent du opto-isolation. En conséquence seule l’isolation entre l’interface de communication et la sortie courant doit être examinée. Ces modules, par exemple S (interface de communication RS485), R (interface de communication RS232) et X3 (sortie en courant linéaire) ont tous besoin d’une alimentation 12V. Si plus d’un de ces modules est installé, afin d’être électriquement isolé, un seul de ces modules peut ne pas disposer d’une isolation. Les autres modules devraient être S4 ou X5 qui ont chacun leur propre alimentation isolée. Par exemple, si un module X3 est installé dans OUTP, dans un objectif d’isolation, on ne devrait installer dans COMM que S4 ou X5.
1.3.5 Description complémentaire sur l’utilisation des modules
Module de sortie en tension
Les modules de sortie en tension tels que V24, V12, V10 ou V5 sont souvent utilisés pour alimenter des transducteurs extérieurs ou la résistance de boucle de retour des transmetteurs. Ces modules peuvent être installés dans n’importe quel emplacement.
Pour standardiser le câblage il est recommandé de les installer dans le premier emplacement libre parmi, dans cet ordre, MIO, AUX et COMM.
Module de commutation sans contact
W1 et W2 sont de nouveaux types de modules de commutation sans contact qui mettent en œuvre la technologie « burn proof » et « zero crossing conduction ». Ils peuvent remplacer la commutation par relais électromécanique avec une plus grande durée de vie et moins de parasites. Ils peuvent considérablement améliorer les parasites dues aux arcs électriques de coupure et améliorer la stabilité et la fiabilité du système. Les éléments de protections sont câblés en série avec les bornes de sortie, ils peuvent contrôler des courants continus jusqu’à 0.2A avec une pointe maximum de courant instantané de 2A. Comme l’élément pilote est un TRIAC, ils sont adaptés à des circuits en 100-240VAC (pas en courant continu) pour des courants allant jusqu’à 80A. Pour des courants supérieurs à 80 A un relais intermédiaire est nécessaire.
Module de commutation par relais électromécaniques
Les modules à relais électromécaniques sont largement utilisés dans le contrôle industriel. Cependant, ils sont les seuls à avoir une durée de vie limitée et des contraintes de volume et ils produisent plus de parasites électromagnétiques. Il est important de choisir un module à relais adapté. Pour contrôler des équipements alimentés en 100~220 VAC, tels que des contacteurs ou des électrovannes, le module W1 est recommandé. Pour contrôler des équipements DC ou AC au-dessus de 50 VAC, on ne peut utiliser que le module à relais. L2 est petit et ses deux bornes normalement ouverte et normalement fermée sont dotées d’absorbeur d’arc électrique, mais leur courant nominal reste faible. Il est adapté aux alarmes. L1 et L3 sont plus gros et adaptés à des courants plus élevés. Dans les instruments de taille 48 mm (par exemple D4, E, F ou E5), on ne peut installer qu’un seul module L1 ou L3. L3 dispose d’une sortie double et peut être utilisé pour prendre en charge deux boucles d’alarme, par exemple AL1+AL2. Si vous n’aimez pas les contacts mécaniques, vous pouvez choisir le module G5 (double pilote SSR) et le connecter à des SSR externes.
1.4. Spécification technique
⬤ Type d’entrées : (l’une quelconque des entrées spécifiées ci-dessous peut être utilisée sélectivement dans un instrument).
Thermocouple : K, S, R, E, J, N, T, B, WRe3-WRe25, WRe5-WRe26.
Détecteur de température à résistance variable : Cu50, Pt100
Tension linéaire : 0~5 V, 0~100 mV, 0~20 mV, 0~500 mV, etc.
Courant linéaire ( un shunt résistif précis externe est requis) : 0~10 mA, 0~20 mA, 4~20 mA, etc.
Entrée étendue (installation du module I4 dans MIO) : 0~20 mA, 4~20 mA ou deux transmetteurs en ligne.
Facultatif : un type additionnel peut être fourni sur demande (l’index de graduation est nécessaire)
⬤ Plage d’entrée de l’instrument
K(-50~1300 ℃), S(-50~1700 ℃), R(-50~1700 ℃), E(0~800 ℃), J(0~1000 ℃), N(0~1300 ℃), T(-200~+350 ℃),
B(200~1800 ℃)
Cu50(-50~+150 ℃), Pt100(-200~+800 ℃)
Entrée linéaire : -9990~30000 définie par l’utilisateur
⚫ Précision de la mesure : 0.25%FS ± 1 unité de mesure
⚫ Résolution : 0.1 ℃ pour K, E, T, N, J, Cu50, Pt100; 1 ℃ pour S et R
⚫ Décalage de température : ≤0.015%FS /℃ (valeur typique 80 ppm/℃)
⚫ Période d’échantillonnage : lit le convertisseur A/D 8 fois par seconde
⚫ Temps de réponse : ≤ 0,5 secondes (quand le paramètre FILt=0)
⚫ Fonction d’alarme : limite haute, limite basse, limite d’écart haute, limite d’écart basse ; assure la fonction de blocage d’alarme à la mise sous-tension.
⚫ Période du contrôle : 0,24 à 300 secondes (valeur à sélectionner) doit être multiple de 0,5 secondes.
⚫ Mode de contrôle :
• Mode de contrôle marche/arrêt (la bande morte est réglable)
• PID standard avec auto-ajustement
• AI PID avec auto-ajustement, par un algorithme d’intelligence artificielle
⚫ Mode de sortie (modulaire)
• Sortie relais électromécaniques (NO+NC) : 250 VAC/2A, 30 VDC/2A, 250 VAC/1A et 30 VDC/1A
• TriAC sortie discrète sans contact (NO ou NC) : 100~ 240 VAC/0.2A (continu), 2A (20mS en pointes instantanées avec une période de répétition ≥5 s)
• Sortie en tension pour pilotage SSR : 12 VDC/30 mA
• Sortie de déclenchement de thyristor à déclenchement et extinction au passage par zéro du courant : peut déclencher un TRIAC de 5~500 A, une paire de SCR montés tête bêche, ou un module de puissance SCR
• Sortie en courant linéaire : 0 ~ 20 mA, 4 ~ 20 mA. Mise à l’échelle par l’utilisateur. (tension de sortie : X3 ≥10,5 V ; X5 ≥7V résistance de charge maximum 500 ohms, précision de sortie 0.2%FS)
⚫ Compatibilité électromagnétique (EMC) : +-4KV/5 kHz en accord avec la norme IEC61000-4-4 ; 4KV en accord avec la norme IEC61000-4-5.
⚫ Tension d’isolation : entre puissance, contacts de relais ou borne de signaux ≥2300VDC ; entre bornes courant faible ≥600 V
⚫ Alimentation : 100~240 VAC,-15 %, +10 % / 50-60Hz ; 120~240 VDC ; ou 24 VDC,-15 %, +10 %.
⚫ Consommation électrique : ≤5 W
⚫ Température ambiante de fonctionnement : -10~60 °C ; humidité ≤90%RH
⚫ Dimensions du panneau avant : 96×96 mm, 160×80 mm, 80×160 mm, 48×96 mm, 96×48 mm, 48×48 mm, 72×72 mm
⚫ Profondeur au-delà de la surface de montage : ≤ 100 mm
1.5. Disposition du bornier arrière et schéma de câblage
Schéma de câblage des instrumentsNote 1 : pour l’entrée en tension linéaire, si la plage est sous les 500 mV, se brancher sur les bornes 19 et 18. Les signaux 0~5 v ou 1~5 V sont raccordés aux bornes 17 et 18.Note 2 : un signal 4~20 mA en courant linéaire peut être transformé en un signal en tension 1~5V en connectant une résistance de 250 ohms et ensuite être raccordé aux bornes 17 et 18. Si un module I4 est installé dans l’emplacement MIO, un signal 4~20 mA peut être raccordé aux bornes 14+ et 15-, et un transmetteur à 2 fils peut être raccordé aux bornes 16+ et 14-.
Note 3 : les fils de compensation des différentes sortes de thermocouples sont différents et doivent être connectés directement aux bornes. Lorsque le mode de compensation interne automatique est utilisé, le fait de connecter le fil commun entre le fil de compensation et les bornes conduit à une erreur de mesure.
Note 4 : lorsque on a sélectionné courant linéaire ou tension de pilotage SSR pour la sortie principale, la sortie se fait sur les bornes 13+, 11-.
Note 2 : un signal 4~20 mA en courant linéaire peut être transformé en un signal en tension 1~5V en connectant une résistance de 250 ohms et ensuite être raccordé aux bornes 11 et 12. Si un module I4 est installé dans l’emplacement MIO, un signal 4~20 mA peut être raccordé aux bornes 14+ et 15-, et un transmetteur à 2 fils peut être raccordé aux bornes 16+ et 14-.
Note 3 : un module S ou S4 peut être installé dans l’emplacement COMM pour la communication. Si un module à relais, TRIAC ou tension de pilotage SSR est installé dans l’emplacement COMM et que le paramètre bAud est défini à 1, on peut commuter entre SV1 et SV2 sur ordre transmis par un contact branché sur les bornes 3 et 4.
Note 4 : (ajoutée par le traducteur) lorsqu’un module G est installé dans l’emplacement OUTP, le SSR
se branche sur les bornes 10+, 8-.
Schéma de câblage des instruments de taille D2
Note 1 : les instruments de taille D2 ne prennent pas en charge une entrée en tension 0~5 V ou 1~5 V. Cependant, ces signaux peuvent être convertis en signaux, respectivement, 0~500 mV ou 100~500 mV en connectant des résistances externes de précision. Un signal 4~20 mA peut être converti en signal 100~500 mV en connectant une résistance de 25 ohms et en se connectant aux bornes 9 et 8.
Note 2 : si un module de communication S ou S4 est installé dans l’emplacement COMM/AUX il peut être utilisé pour la communication. Si un module L2 y est installé, et que le paramètre bAud =0, on peut l’utiliser pour la sortie des alarmes AU1 et AU2 ; si le paramètre bAud=2, on peut l’utiliser pour les alarmes AU1 et AL1. Si un module L1, L2, L4, G, K1, W1 ou W2 y est installé, il peut servir de sortie auxiliaire dans un système de contrôle bidirectionnel (chauffage / réfrigération). Si un module I2 y est installé et que bAud=1, alors on peut y raccorder un contact entre les bornes 3 et 5 pour commuter entre SP1 et SP2 (AI+518) ou pour commuter le programme entre les états Marche et Arrêt (AI-518P)
Note : les instruments de taille D5 montables sur rail DIN disposent d’un canal pour la fonction d’alarme et de communication. On peut installer un module G, X5, L2, K1, K5, K6 ou W1 dans l’emplacement OUTP.
Note 1 : pour les entrées en tension linéaire en dessous de 500 mV, se connecter aux bornes 11+ et 10-. Pour les entrées 0~5 V ou 1~5 V, se connecter aux bornes 9+ et 10-. Un signal 4~20 mA peut être converti en 1~5 V à l’aide d’une résistance de 250 ohms et raccordé aux bornes 9+ et 10+.
Note 2 : lorsqu’un module L3 est installé dans l’emplacement COMM/AUX, il dispose de deux canaux d’alarme. Si c’est un module SL il n’en a qu’un seul.
Note 1 : selon la charge et la tension, choisissez un varistor adapté pour protéger le thyristor. Un circuit RC est requis pour les charges inductives ou les sorties à déclenchement par déphasage.
Note 2 : un module SCR de puissance est recommandé. Un module de puissance inclut deux SCRs comme présentés dans le rectangle en pointillé.
Note 3 : les modules TRIAC K5 et K6 ne sont compatibles qu’avec des alimentations 220~380 VAC en 50 Hz.
NOTICE : DEUXIÈME PARTIE — AFFICHAGES ET MODES OPÉRATOIRES (afficher ☛)
2. AFFICHAGE ET MODES OPÉRATOIRES
2.1. Description du panneau avant
1 – Afficheur supérieur : affiche la valeur de la mesure (Process value), du code du paramètre, etc.2 – Afficheur inférieur : affiche le point de consigne (Set value SV), la valeur d'un paramètre ou un message d'alarme
3 – ↻ Touche de réglage : pour accéder à la table des paramètres et confirmer la modification d'un paramètre
4 – ◁ Touche de déplacement ou de démarrage de l'auto-ajustement
5 – ▽ Touche de décrémentation ou de démarrage du programme
6 – △ Touche d'incrémentation ou d'arrêt du programme
Voyants:
MAN ne s'applique pas à la série AI-518
PRG allumé signifie que le programme est en exécution
MIO, OP1, OP2, AL1, AL2, AU1 ou AU2 indiquent qu'une opération d'entrée sortie est en cours sur le module correspondant. Par exemple, lorsque COMM est allumé l'instrument est en communication avec l'ordinateur
État d'affichage de base : lorsque l'appareil est alimenté, l'afficheur supérieur affiche la valeur de la mesure (PV) et l'afficheur inférieur affiche la consigne (SV). Cet état est appelé « État d'affichage de base ».
On a vu que l'afficheur du bas peut afficher des messages. En voici la codification :
Symbol | Description | ||
---|---|---|---|
orAL | La spécification de l'entrée (sonde) est incorrecte ou la sonde est déconnectée ou en court-circuit | ||
HIAL | Alarme de limite haute | ||
LoAL | Alarme de limite basse | ||
HdAL | Alarme d'écart haut (high deviation) | ||
LdAL | Alarme d'écart bas (low deviation) | ||
EErr | Erreur logicielle IC | ||
8888 | Erreur logicielle IC |
Note 1 : les messages d'alarme peuvent être inhibés en mettant le paramètre AdIS sur OFF.
Note 1 : lorsqu'une alarme orAL se produit, la sortie est coupée un court instant
Note 3 : pour AI-518P, les messages StoP, HoLd et rdy signifie Arrêt, en suspens et prêt.
2.2. Diagramme de flux du réglage des paramètres
2.3. Description des opérations
2.3.3 Réglage des paramètres
Dans l'état d'affichage de base, un appui de 2 secondes sur la touche ↻ permet d'accéder à la table des paramètres.
Un appui bref sur ↻ permet de passer au paramètre suivant. Les touches ◁ , ▽ ou △ servent à modifier un paramètre. Un appui prolongé sur ◁ permet de revenir au paramètre précédent.
Un appui sur ◁ + ↻ (+ signifiant l'un puis les deux ensemble) permet de sortir de la table des paramètres. L'appareil sort automatiquement de la table des paramètres si aucune touche n'est utilisée pendant 25 secondes. Dans ce cas, le dernier paramètre modifié n'est pas sauvegardé.
Dans la table des paramètres, fixer le dernier paramètres Loc à 808 et appuyer ensuite sur ↻ permet d'accéder à la table des paramètres Système.
2.3.2 Réglage du point de consigne
Dans l'état d'affichage de base, si le paramètre Loc n'est pas verrouillé (locked), on peut régler la consigne en appuyant d'abord sur ◁ puis en appuyant sur ◁ , ▽ ou △ pour ajuster la valeur. ▽ décrémente la valeur, △ incrémente la valeur et ◁ permet de sélectionner le chiffre à modifier. Un appui prolongé sur △ ou ▽ accélère l'incrémentation ou la décrémentation. La plage de réglage de la consigne est limitée par les paramètres SPL et SPH. Les valeurs par défaut de ces limites sont 0 et 400.
Réglage des pas de programme
Appuyer sur ◁ depuis l'état d'affichage de base. L'instrument entre dans le mode de réglage du programme. La consigne du pas de programme courant est affiché. Les touches ◁ , ▽ ou △ servent à modifier la valeur.
La touche ↻ permet de passer au paramètre suivant. Les paramètres du programme sont des séquences de consigne1, temps1, consigne2, temps2.
Un appui de 2 secondes sur ◁ permet de revenir au paramètre précédent. Les pas de programme peuvent être modifiés à tout moment, même si le programme est en cours d'exécution.
Marche / suspension (seulement pour le modèle AI-518P)
Dans le mode d'affichage de base, si le programme est dans l'état Stop (arrêté), StoP clignote dans l'afficheur inférieur. Appuyer sur ▽ pendant 2 secondes environ jusqu'à ce que l'afficheur inférieur affiche Run. Le programme démarre.
Si la valeur F du paramètre PAF est 1, l'utilisateur peut maintenir la touche ▽ durant environ 2 secondes pour passer à l'état suspendu (HoLd). Si la valeur F du paramètre PAF est 0 l'état suspendu (HoLd) ne peut être activé qu'en mettant le paramètre Srun à HoLd.
Dans l'état suspendu (HoLd) le programme continue à maintenir la consigne à la valeur de consigne du pas en cours mais le compteur de temps (timer) est arrêté.
Pour redémarrer le programme en mode normal, maintenir la touche ▽ enfoncée environ 2 secondes jusqu'à ce que l'afficheur inférieur affiche Run.
Arrêt
Dans le mode d'affichage de base, maintenir la touche △ pendant environ 2 secondes jusqu'à ce que l'afficheur inférieur affiche stoP. Le programme est arrếté, le compteur de temps (timer) est remis à zéro et arrêté, le numéro du pas StEP est remis à 1 et la sortie est coupée.
2.3.3 Auto-ajustement(auto tuning)
Une fois la méthode de contrôle choisie (CtrL=APId / nPId), les paramètres du PID peuvent être auto-ajustés en lançant le mode auto-ajustement(auto-tuning).
Dans l'état d'affichage de base, appuyer sur la touche ◁ durant 2 secondes environ pour faire apparaître le paramètre At. Appuyer sur △ pour passer la valeur de At de oFF à on. Ensuite appuyer sur ↻ pour démarrer le processus d'apprentissage. Durant cet auto-ajustement, l'appareil exécute des marche/arrêt (sur la sortie). Après 2 ou 3 cycles, l'appareil en déduit les paramètres de contrôle optimaux.
Si vous désirez sortir de l'auto-ajustement maintenez la touche ◁ pendant 2 secondes environ pour faire apparaître de nouveau le paramètre At. Modifiez At de on à oFF et appuyez sur la touche ↻ pour confirmer. L'auto-ajustement est annulé. (P.S. Si le paramètre “SPr” est activé et que le chauffage était en cours, alors At (l'auto-tuning) est arrêté jusqu'à ce que la temperature soit atteinte). Si le mode de contrôle concerne un système dual chauffage / réfrigération les paramètres PID sont séparés en deux groupes pour l'apprentissage. Lorsque l'appareil est en train de refroidir depuis AUX on peut alors activer l'auto-ajustement pour obtenir les valeurs optimales de P2, I2 et d2.
Note 1 : pour AI-518P si l'auto-ajustementest en cours, le compteur de temps est stoppé jusqu'à la fin de l'apprentissage.
Note 2 : si la consigne est différente, les paramètres appris sont probablement différents, c'est pourquoi il est préférable de régler la consigne à une valeur couramment utilisée ou une valeur moyenne d'abord avant de lancer l'apprentissage. Pour les fours bien isolés thermiquement, la consigne peut être mise à la plus haute température applicable. Selon le système contrôlé l'auto-ajustementpeut prendre des secondes ou des heures.
Note 3 : le paramètre CHYS (différentiel de marche arrêt, hystérisis) influence la précision de l'apprentissage. En général, des valeurs faibles de CHYS donnent une meilleure précision des résultats d'apprentissage. Des valeurs trop importantes rendent le système incontrôlable. La valeur recommandée est 2.0.
Note 4 : tous les appareils disposent de la fonction d'auto-adaptation. C'est à dire qu'ils sont capables d'apprendre le système contrôlé durant le fonctionnement. Le contrôle lors de la première exécution avec les paramètres appris n'est probablement pas parfait., mais les choses vont s'améliorant après plusieurs exécutions grâce à l'auto-adaptation.
Paramètres et réglages
Verrouillage des paramètres (Loc) et paramètres de champ
L'accès aux paramètres est protégé par le paramètre Loc afin d'éviter des erreurs. Les fonctions sont montrées comme suit :
- √ autorise la modification de la donnée ou l'exécution
- ✗ interdit la modification de la donnée ou l'exécution
Les fonctions Run (marche), Stop (arrêt) , Hold (suspendu) et Program Time & Temp (durée de pas et température) s'appliquent uniquement à la série AI-518P
Loc | SV | AT | Paramètre
primaire |
Paramètre
secondaire |
Changement d'état à Run
(marche), Stop (arrêt) ou Hold (suspendu) |
Durée de pas de programme & température |
---|---|---|---|---|---|---|
0 | √ | √ | √ | ✗ | √ | √ |
1 | √ | ✗ | √ | ✗ | ✗ | √ |
2 | ✗ | ✗ | √ | ✗ | √ | ✗ |
3 | ✗ | ✗ | √ | ✗ | ✗ | ✗ |
4 - 255 | ✗ | ✗ | ✗ | ✗ | ✗ | ✗ |
808 | √ | √ | √ | √ | √ | √ |
Loc 808 est le mot de passe maître. Cette valeur peut être modifiée en modifiant le paramètre PASd (mot de passe) . Définissez le paramètre PASd avec prudence, si vous le perdez vous ne pourrez plus accéder à la table des paramètres.
On peut définir 1 à 8 paramètres de champs en réglant les paramètres EP1 à EP8. Si le nombre de paramètres de champ utilisés est inférieur à 8, le premier premier paramètre de champ inutilisé doit être mis à nonE.
Les valeurs initiales des paramètres de champ sont :
- EP1=HIAL
- EP2=LoAL
- EP3=HdAL
- EP4=LdAL
les autres sont égaux à nonE
La valeur initiale de Loc est 0.
Vous pouvez définir les paramètres de champ et Loc pour modifier le style des opérations. Par exemple, vous pouvez exécuter l'auto-ajustement(auto tuning) depuis un paramètre de champ plutôt que par un appui sur la touche ◁ dans l'état d'affichage de base et ne prendre que HIAL et HdAL comme paramètres de champ.
Les paramètres EP et Loc devraient être positionnés comme suit :
- EP1=HIAL
- EP2=HdAL
- EP3=At
- EP4=nonE
- Loc=1
NOTICE : TROISIÈME PARTIE — LA TABLE DES PARAMÈTRES (afficher ☛)
La table des paramètres
La table des paramètres peut être divisée en 8 groupes : alarmes, contrôles, entrées, sorties, communication, système, consignes et paramètre de champ. Nous les présentons ci-après l'un après l'autre.Note : les valeurs que j'ai retenues sont en rouge dans la colonne plage de réglage. ?? indique que la valeur est modifiable. L'absence de valeur en rouge signifie que le choix est indifférent.
Code | Nom | Description | Plage de réglage | ||||||||||||||||||||||||||||||||||||||||||||||||||||||||||||||||||||
---|---|---|---|---|---|---|---|---|---|---|---|---|---|---|---|---|---|---|---|---|---|---|---|---|---|---|---|---|---|---|---|---|---|---|---|---|---|---|---|---|---|---|---|---|---|---|---|---|---|---|---|---|---|---|---|---|---|---|---|---|---|---|---|---|---|---|---|---|---|---|---|
HIAL | High limit alarm
Alarme de limite haute |
Alarme s'active quand PV>HIAL
Alarme se désactivé quand PV<HIAL-AHYS Le comportement de la sortie associée est définie par le paramètre AOP. |
-9990 à 32000 unités
110 °C (230 °F) | ||||||||||||||||||||||||||||||||||||||||||||||||||||||||||||||||||||
LoAL | Low limit alarm
Alarme de limite basse |
L'alarme s'active quand PV devient inférieure à LoAL.
L'alarme se désactive lorsque PV devient supérieur à LoAL+AHYS Lorsque la valeur est définie à Min. la fonction est désactivée. |
-9990 à 32000 unités
0 °C (32 °F) | ||||||||||||||||||||||||||||||||||||||||||||||||||||||||||||||||||||
HdAL | Deviation high alarm
Alarme d'écart haut |
L'alarme s'active lorsque l'écart PV-SV devient supérieur à HdAL
L'alarme se désactive lorsque l'écart devient inférieur à HdAL-AHYS |
-9990 à 32000 unités
1°C (1,8)°F) | ||||||||||||||||||||||||||||||||||||||||||||||||||||||||||||||||||||
LdAL | Deviation low alarm
Alarme d'écart bas |
L'alarme s'active lorsque l'écart PV-SV devient inférieur à LdAL
L'alarme se désactive lorsque l'écart PV-SV devient supérieur à LdAL+AHYS Lorsque la valeur est définie à Min. la fonction est désactivée. HdAL et LoAL peuvent aussi être utilisées comme limite haute et basse si besoin (voir la description du paramètre AF). |
-9990 à 32000 unités
-0,3 °C (-0,5°F) | ||||||||||||||||||||||||||||||||||||||||||||||||||||||||||||||||||||
AHYS | Hystérésis d'alarme | Évite la commutation trop rapide des alarmes lorsque PV fluctue | 0 à 2000 unités
0 | ||||||||||||||||||||||||||||||||||||||||||||||||||||||||||||||||||||
AdIS | Affichage des alarmes | oFF : n'affiche pas les alarmes dans l'afficheur inférieur
on : affiche le message d'alrame dans l'afficheur inférieur en alternance |
on | ||||||||||||||||||||||||||||||||||||||||||||||||||||||||||||||||||||
AOP | Affectation des sorties d'alarme |
Exemple AOP=3301 indique que HdAL et LdAL sont envoyées sur AU1, que LoAL n'a pas de sortie et que HIAL est envoyée sur AL1
Note 2 : l'installation d'un module L3 de relais double dans ALM ou AUX peut implémenter les alarmes AL2 ou AU2 |
0 à 4444
| ||||||||||||||||||||||||||||||||||||||||||||||||||||||||||||||||||||
Ctrl | Mode de contrôle | onoF : mode de contrôle on/off, pour des situations ne requérant pas une grande précision
APId : PID avec Intelligence artificielle avancée (advanced artificial intelligence ) (recommandé) nPId : algorithme PID standard avec la fonction anti-saturation de l'intégrale (pas d'intégration de l'erreur PV -SV à l'extérieur de la bande proportionnelle) POP : Transmetteur de PV L'appareil fonctionne comme un transmetteur de température SOP : Transmetteur de SV. L'appareil fonctionne come un générateur de programme |
onoF
APId nPId POP SOP | ||||||||||||||||||||||||||||||||||||||||||||||||||||||||||||||||||||
Srun | État d'exécution | run : le contrôle ou le programme s'exécute . Le voyant PRG est allumé
StoP : le contrôle ou le programme sont arrêtés. Le voyant PRG est éteint et l'afficheur inférieur affiche StoP en alternance. HoLd : uniquement sur AI-518P . Lorsque l'état suspendu (HoLd) apparaît la température est maintenue. Si le paramètre Pno=0 (mode sans limitation de temps), le contrôleur fonctionne comme AI-518. Si Pno >0 (en mode programme) et que Srun est défini à HoLd le compteur de temps s'arrête et la température est maintenue. Un appui sur Hold sur le panneau avant reprend le comptage. |
StoP
run HoLd ?? (intervention sur le panneau de commande) | ||||||||||||||||||||||||||||||||||||||||||||||||||||||||||||||||||||
Act | Méthode d'action | rE : action inverse. Une augmentation de la mesure produit une diminution de la sortie, comme dans le cas du chauffage
dr : action directe. Une augmentation de la mesure produit une augmentation de la sortie, comme dans le cas d'une réfrigération. rEbA : action inverse avec une alarme sur limite basse et une alarme sur limite basse d'écart bloquant à la mise sous énergie. drbA : action directe avec une alarme sur limite haute et une alarme sur limite haute d'écart bloquant à la mise sous énergie. |
rE
dr rEbA drbA | ||||||||||||||||||||||||||||||||||||||||||||||||||||||||||||||||||||
At | Auto tuning
Apprentissage |
oFF : la fonction d'auto-ajustement est hors service
on : la fonction d'auto-ajustementest en service pour calculer les valeurs. FoFF : la fonction d'auto-ajustementest hors service est il impossible de l'activer en appuyant sur une touche du panneau de commande. |
oFF
on FoFF ?? (intervention sur panneau de commande) | ||||||||||||||||||||||||||||||||||||||||||||||||||||||||||||||||||||
P | Bande proportionnelle | La bande proportionnelle dans le contrôle PID ou APID. Au lieu de pourcentage de la plage de mesure, l'unité est la même que PV.
Généralement P,I, D et Ctl peuvent être obtenus par apprentissage. Ils peuvent également être entrés à la main, si vous connaissez déjà les valeurs correctes. |
1 à 32000 umités | ||||||||||||||||||||||||||||||||||||||||||||||||||||||||||||||||||||
I | Constante de temps intégrale | Pas d'action intégrale lorsque I est à 0. | 0 à 9999 secondes | ||||||||||||||||||||||||||||||||||||||||||||||||||||||||||||||||||||
d | Constante de temps dérivée | Pas d'action dérivée lorsque d est à 0 | o à 999.9 secondes | ||||||||||||||||||||||||||||||||||||||||||||||||||||||||||||||||||||
Ctl | Période du contrôle | Une faible valeur améliore la précision.
Pour le cas des sorties SSR, thyristor ou contrôle linéaire en courant, c'est généralement entre 0.5 et 3 secondes. Pour une sortie relais, dans un système à deux sorties chauffage/réfrigération c'est généralement entre 15 et 40 secondes car de faibles valeurs entraîneraient une sollicitation mécanique trop fréquente des relais et du chauffage/réfrigération raccourcissant la durée de vie. Une recommandation est que Ctl soit entre 1/5 et 1/10 de la constante de temps dérivée. (cela devrait être des temps d'intégration de 0.5 secondes). Lorsque le paramètre OPt ou Aut = rELy, Ctl est limité à plus de 3 secondes. L'auto-ajustementdevrait automatiquement définir Ctl à une valeur adaptée prenant en considération la précision du contrôle et la longévité des relais mécaniques. Lorsque le paramètre CtrL = onoF, Ctl est utilisé comme un comme un temps minimum avant une remise sous tension. Ce fonctionnement est adapté aux compresseurs. |
0.2 à 300 secondes
2 | ||||||||||||||||||||||||||||||||||||||||||||||||||||||||||||||||||||
P2 | 2e bande proportionnelle | La 2e bande proportionnelle dans le contrôle PID et APID. Au lieu de pourcentage de la plage de mesure, l'unité est la même que PV.
Généralement P,I, D et Ctl peuvent être obtenus par apprentissage. Ils peuvent également être entrés à la main, si vous connaissez déjà les valeurs correctes. |
1 à 32000 unités. | ||||||||||||||||||||||||||||||||||||||||||||||||||||||||||||||||||||
I2 | 2e constante de temps intégrale | Pas d'action intégrale lorsque I est à 0. | 0 à 9999 secondes | ||||||||||||||||||||||||||||||||||||||||||||||||||||||||||||||||||||
d2 | 2e constante de temps dérivée | Pas d'action dérivée lorsque d est à 0 | 0 à 99.9 secondes | ||||||||||||||||||||||||||||||||||||||||||||||||||||||||||||||||||||
Ctl2 | 2e période de contrôle | Même chose que pour Ctl | 0.2 à 300.0 secondes | ||||||||||||||||||||||||||||||||||||||||||||||||||||||||||||||||||||
CHYS | Hystérésis du contrôle | CHYS est utilisé dans le mode de contrôle on-off afin d'éviter une sollicitation trop fréquente des relais..
Pour un système a action inverse (chauffage), lorsque PV devient supérieur à SV, la sortie est coupée (off), lorsque PV devient inférieur à SV-CHYS elle est rétablie (on). Pour un système à action directe (réfrigération) lorsque PV devient inférieur à SV la sortie est coupée (off) lorsque PV devient supérieur à SV+CHYS elle est rétablie (on) |
0 à 2000
0 | ||||||||||||||||||||||||||||||||||||||||||||||||||||||||||||||||||||
InP | Spécification de type d'entrée |
|
21 | ||||||||||||||||||||||||||||||||||||||||||||||||||||||||||||||||||||
dPt | Résolution d'affichage | On peut choisir entre quatre formats (0, 0.0,0.00,0.000).
Note 1 : pour les entrées thermocouples ou RTD, on ne peut sélectionner que 0 ou 0.0 et la résolution interne est 0.1. Lorsqu'un thermocouple de type S est utilisé, il est recommandé d'avoir dPt à 0. Si le type d'entrée spécifié (InP) est 17, 18 ou 22 on peut utiliser 0.0 ou 0.000. |
0
0.0 0.00 0.000 | ||||||||||||||||||||||||||||||||||||||||||||||||||||||||||||||||||||
ScL | Limite basse du signal d'entrée | Définit la limite basse du signal d'entrée. Cette valeur limite également le signal transmis lorsque l'appareil est utilisé en transmetteur (CtrL =POP ou SOP) ainsi que l'affichage lumineux. | -9990 à +32000 unités | ||||||||||||||||||||||||||||||||||||||||||||||||||||||||||||||||||||
ScH | Limite haute du signal d'entrée | Définit la limite haute du signal d'entrée. Cette valeur limite également le signal transmis lorsque l'appareil est utilisé en transmetteur (CtrL =POP ou SOP) ainsi que l'affichage lumineux. | |||||||||||||||||||||||||||||||||||||||||||||||||||||||||||||||||||||
Scb | Décalage de l'entrée | Scb est utilisé pour compenser l'erreur due au transducteur, signal d'entrée ou de la jonction froide du thermocouple.
PV après compensation = PV before compensation +Scb Cette valeur vaut généralement 0. Un réglage incorrect conduit à des mesures inexactes. |
-1999 à +4000 unités
0 | ||||||||||||||||||||||||||||||||||||||||||||||||||||||||||||||||||||
FILt | Filtre d'entrée PV | La valeur de FILt détermine la capacité à filtrer le bruit.
Lorsqu'on utilise une valeur élevée, la mesure est stabilisée mais la réponse est lente. En général, cette valeur peut être fixée entre 1 et 3. S'il existe de grandes interférences, on peut l'augmenter graduellement pour rendre les fluctuations de la mesure inférieures à 2 à 5. Lorsque l'instrument est vérifié météorologiquement FILt peut être mis à 0 ou 1 pour réduire le temps de réponse. |
0 | ||||||||||||||||||||||||||||||||||||||||||||||||||||||||||||||||||||
Fru | Sélection de la fréquence d'alimentation et de l'échelle de température | 50C : 50 Hz, affichage en °C,
50F : 50 Hz, affichage en °F 60C: 60 Hz, affichage en °C 60F: 60 Hz, affichage en °F L'entrée est mieux prémunie des interférences avec la fréquence 50 ou 60Hz lorsque ce paramètre est défini. |
50C
50F 60C 60F | ||||||||||||||||||||||||||||||||||||||||||||||||||||||||||||||||||||
OPt | Type de l'entrée principale | SSr : tension de sortie pour pilotage d'un SSr ou signal de déclenchement d'un thyristor par passage par zéro du courant. Un module S, K1 ou K3 doit être installé. La puissance de sortie est réglée par le rapport cyclique temporel on-off. La période Ctl étant en général définie entre 0.5 et 4 secondes.
|
SSr
rELy 0-20 4-20 PHA | ||||||||||||||||||||||||||||||||||||||||||||||||||||||||||||||||||||
Aut | Type de sortie auxiliaire | Ne définir AUX que lorsque AUX est utilisé comme sortie auxiliaire d'un système bidirectionnel chauffage/réfrigération.
SSr : tension de sortie pour pilotage d'un SSr ou signal de déclenchement d'un thyristor par passage par zéro du courant. Un module S, K1 ou K3 doit être installé. La puissance de sortie est réglée par le rapport cyclique temporel on-off. La période Ctl étant en général définie entre 0.5 et 4 secondes.
|
SSr
rELy 0-20 4-20 | ||||||||||||||||||||||||||||||||||||||||||||||||||||||||||||||||||||
OPL | Limite basse de la sortie | 0~100% : OPL est la sortie minimum de OUTP dans système de contrôle unidirectionnel.
-1~ -100% : le système fonctionne en bidirectionnel avec deux sorties. Lorsque ACt=rE ou rEbA, OUTP (la sortie principale) concerne le chauffage et AUX (la sortie auxiliaire) concerne la réfrigération Les rôles sont inversés sir Act=dr ou drbA Dans un système bidirectionnel, OPL limite la sortie de refroidissement. Aussi, lorsque OPL=-100% la sortie réfrigération n'est pas limitée. Une valeur d'OPL à -110% permet de dépasser la valeur maxi de la sortie de 10%. Dans le cas d'une sortie SSR on ne doit pas dépasser une valeur de 100%. |
-110 à +100%
0 | ||||||||||||||||||||||||||||||||||||||||||||||||||||||||||||||||||||
OPH | Limite haute de la sortie | OPL limite la sortie OUTP (sortie principale) lorsque PV<OEF. OPH doit être supérieur à OPL. | 0~110%
100 (sera réglé lors de l'ébullition) | ||||||||||||||||||||||||||||||||||||||||||||||||||||||||||||||||||||
OEF | Plage de fonctionnement de OPH | Lorsque PV<OEF, la limite haute de OUTP est OPH. Lorsque PV> OEF la limite haute de OUTP est 100%.
Par exemple, pour éviter une élévation trop rapide de la température sous 150 °C, on peut forcer un chauffage à travailler à 30% de la puissance maximum . Dans ce cas on règle OEF=150 °C et OPH=30 (%). |
110°C (230 °F) pour autoriser le réglage de la puissance en ébullition | ||||||||||||||||||||||||||||||||||||||||||||||||||||||||||||||||||||
Addr | Communication address | Sur la ligne de communication, des appareils différents doivent avoir des adresses différentes | 0 à 80 | ||||||||||||||||||||||||||||||||||||||||||||||||||||||||||||||||||||
bAud | Débit de bits | Le débit de bits .doit être entre 1200 et 19200 bits/secondes. Lorsque l'emplacement COMM/AUX est utilisé comme AUX, bAud doit être mis à 0.
Pour des appareils de taille D2, si bAud=2, on peut l'utiliser pour une sortie d'alarme AU1+AL1. Cela s'applique à la fonction de sortie d'événement parce que une sortie d'événement ne peut se faire que sur AL1 et AL2. Pour des appareils de taille D2, is I2 est installé et que bAud=1 , alors il peut recevoir des signaux d'entrée on-off pour commuter SV1 et SV2 (AI-518) ou commuter l'état du programme RUN/Stop (marche/arrêt) (AI-518P) en connectant un interrupteur entre les bornes 3 et 5. |
0 à 19,2
Kbits/secondes | ||||||||||||||||||||||||||||||||||||||||||||||||||||||||||||||||||||
Et | Type d'événement d'entrée | Lorsque le module I2 est installé, l'appareil présente les fonctions suivantes:
nonE : désactive la fonction d'entrée d'événement reSt : fonction de commutation marche/arrêt. Une fermeture du contact brève démarre le programme, une fermeture de plus de 2 secondes l'arrête. SP1.2 : fonction de commutation entre les consignes SV1 et SV2 (AI-518 ou AI-518P avec Pno=0). Si le contact est ouvert SV=SP1 s'il est fermé SV=SP2 PId2 : fonction de commutation entre le 1er PID et le 2e PID. Lorsqu'utilisé dans un système unidirectionnel, si le contact est ouvert, P, I, d et Ctl sont actifs, s'il est fermé c'est P2, I2, d2 et Ctl2 qui le sont. |
nonE
reSt SP1.2 PId2 | ||||||||||||||||||||||||||||||||||||||||||||||||||||||||||||||||||||
AF | Fonction avancée | AF permet de sélectionner la fonction avancée. La valeur de AF se calcule comme suit:
AF=Ax1 + Bx2 + Cx4 + Dx8 + Ex16 + Fx32 + Gx64 A=0 : HdAL et LdAL fonctionnent comme des alarmes de limite 'écart haute et basse A=1 : HdAL et LdAL fonctionnent comme des alarmes de limite haute et basse de la mesure et l'appareil peut avoir deux groupes d'alarme de limites haute et basse
B=1 comme hystérésis bilatéral.
C=1 : la barre lumineuse indique la mesure (pour des appareils munis de cette barre uniquement)
D=1 : Loc=PASd donne accès à la table des paramètres.
E=1 : HIAL et LoAL deviennent des alarmes d'écart haut et bas
times. When on linear input mode, biggest display value is 3200 units F=1 : mode de large plage d'affichage. Lorsque la valeur est supérieure à 3200, choisir cette option.
G=1 Lorsque le thermocouple ou la RTD est cramé, PV augmente mais l'alarme n'est pas déclenchée. Après avoir été définie l'alarme de limite haute dispose d'un délai de 30 secondes avant de passer en fonctionnement normal. Note : AF=0 est recommandé |
0 | ||||||||||||||||||||||||||||||||||||||||||||||||||||||||||||||||||||
PASd | Mot de passe | Lorsque PASd=0 à 255 ou lorsque AF.D=0, positionner Loc à 808 permet d'accéder à toute la table des paramètres.
Lorsque PASd= 256 à 9999 et AF.D=1, seul Loc=PASd permet d'accéder à toute la table des paramètres. Soyez prudents, si le mot de passe est perdu, vous ne pourrez plus accéder à la table. |
0 à 9999
0 | ||||||||||||||||||||||||||||||||||||||||||||||||||||||||||||||||||||
SPL | Limite basse de SV | Valeur minimum que SV (la consigne) est autorisée à prendre. | -999 à +3000 unités
0 | ||||||||||||||||||||||||||||||||||||||||||||||||||||||||||||||||||||
SPH | Limite haute de SV | Valeur maximum que SV est autorisée à prendre | 110 °C (240 °F) | ||||||||||||||||||||||||||||||||||||||||||||||||||||||||||||||||||||
SP1 | Consigne 1 | Lorsque Pno=0 ou 1 alors SV=SP1 | SPL à SPH | ||||||||||||||||||||||||||||||||||||||||||||||||||||||||||||||||||||
SP2 | Consigne 2 | Lorsqu'un module I2 est installé dans l'emplacement MIO, on peut utiliser un commutateur extérieur (contact) pour passer de SP1 à SP2 et inversement. Si le contact est ouvert, SV=SP1, s'il est fermé SV=SP2. | |||||||||||||||||||||||||||||||||||||||||||||||||||||||||||||||||||||
SPr | Limite de pente (uniquement AI-518P) | Un fois SPr défini, si PV<SV le programme démarre. Le premier pas de rampe est limité par SPr jusqu'à ce que la température atteigne la première valeur de consigne. Durant tout ce temps le voyant RUN clignote.
Dans le mode Ramp, SPR n'a d'effet que sur le premier pas Dans le mode Soak (trempage), SPr a de l'effet sur tous les pas. |
0~3200 °C / min.
?? | ||||||||||||||||||||||||||||||||||||||||||||||||||||||||||||||||||||
Pno | Numéro du pas de programme (AI-518P seulement) | Pour définir le numéro du pas de programme en exécution.
Pno=0 arrête le mode programme et l'appareil se comporte comme AI-518. Néanmoins SPr continue à limiter la pente des rampes. Pno=1~30 fonctionnement normal du AI-518P |
0~30
?? | ||||||||||||||||||||||||||||||||||||||||||||||||||||||||||||||||||||
PonP | Mode d'exécution du programme après un rétablissement de l'alimentation (AI-518P) | Cont: continue à exécuter le programme à partir du point d'interruption. Si l'état arrêté été activé avant la coupure d'alimentation, le programme en état arrêté.
StoP : arrête le programme au rétablissement de l'alimentation run1 : redémarre au pas 1 sauf si l'état était arrêté. dASt : si l'alarme d'écart est activé à la reprise, alors arrête le programme, autrement reprend au point d'interruption. HoLd : va à l'état suspendu au rétablissement de l'alimentation sauf si on était à l'état arrêté. |
Cont
StoP run1 dASt HoLd | ||||||||||||||||||||||||||||||||||||||||||||||||||||||||||||||||||||
PAF | Mode d'exécution du programme (AI-518P) | PAF = Ax1 + Bx2 + Cx4 + Dx8 + Ex16 + Fx32
When A=0 : désactive la fonction préparation (rdy) A=1 : active la fonction préparation (ceci est l'inverse de ce que prétend la doc. en anglais à cette date) B=0 : mode Ramp (rampe) B=1 : mode Soak (trempage) C=0 : unité de temps en minutes, la plage est 0.1~3200. C=1 : unité de temps en heures, la plage est 0.1~3200 D=0 : désactive la fonction PV startup (PV démarrage) D=1 : active la fonction PV start up (PV démarrage) E=0 : lors de l'utilisation en générateur de programme , l'afficheur supérieur affiche PV E=1 : lors de l'utilisation en générateur de programme , l'afficheur supérieur affiche le pas de programme courant. F=0 : mode opératoire standard de la commutation suspendu / en marche F=1 : on peut commuter les états suspendu / en marche sur le panneau avant
|
35 | ||||||||||||||||||||||||||||||||||||||||||||||||||||||||||||||||||||
EP1 ~ EP8 | Définition des paramètres de champs | Définit 0~8 paramètres en tant que paramètres de champ | nonE et tous les codes de paramètre |
MISE EN BOÎTE
J'ai finalement opté pour des prises sur l'appareil sur lesquelles viennent se raccorder les câbles sonde et commande SSR issus d'un boîtier séparable.
Les prises sont des prises aviation (autour de 3 € prise et fiche). Voici deux photos du boîtier (face avant et face arrière)
Note : pour percer les trous des presse-étoupes, j'ai utilisé le foret étagé que je m'étais procuré pour les essais du CR20. La découpe de la plaque avant a été faite à la scie sauteuse en fixant préalablement la plaque sur une plaque de contreplaqué de 5mm avec quatre vis. Il faut être précautionneux parce qu'elle est assez fine.
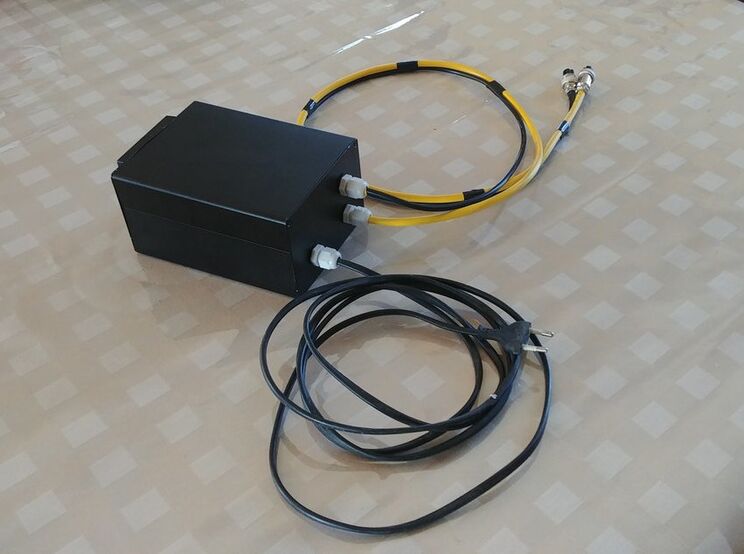
En fin d'article je laisse un inventaire des pièces utilisées avec leur coût et leur provenance.
PARAMÉTRAGE
Paramétrage
Avant d'aborder le paramétrage, il convient de bien comprendre comment se fait l'accès à ces paramètres.
Il y a deux sortes de paramètres :
- les paramètres à accès libre,
- les paramètres à accès par mot de passe.
Paramètres à accès libre
On y accède par un appui de 2 secondes sur la touche ↻. Les touches fléchées permettent d'en modifier la valeur et un appui bref sur la touche ↻ permet de passer au paramètre suivant.
Un appui de deux secondes sur la touche ◁ permet de revenir sur le paramètre précédent.
Ces paramètres sont choisis par indirection à partir des paramètres dit « de champ » EP1 à EP8. Il faut donc d'abord accéder à la liste complète des paramètres (avec mot de passe) pour les définir.
À l'origine ils sont définis comme suit :
- EP1=HIAL
- EP2=LoAL
- EP3=HdAL
- EP4=LdAL
Personnellement pour l'usage que je compte faire de l'appareil, je les règle comme suit et explique pourquoi :
- EP1 =Pno En effet le paramètre Pno à 0 fait fonctionner l'appareil sans programme, ce qui est utile à la mise au point du PID.
- EP2= OPH . Lors d'une séance de brassage, une fois l'ébullition atteinte, on pourra régler la puissance de chauffe avec ce paramètre 0 à 100 %, on conjonction avec le paramètre OEF réglé une fois pour toute au delà de 110 °C ou 230 °F.
- EP3=P
- EP4 = I
- EP5=d pour mise au point du PID
- EP6=Ctrl pour choisir entre les modes nPID et PID
- EP7=FILt pour régler le filtrage d'entrée
- EP8 = nonE pas utilisé
Une fois un paramètre affiché on peut régler sa valeur avec les touches fléchées puis passer au paramètre suivant par un appui sur la touche ↻.
En fin de liste on arrive sur Loc. Si on y entre le mot de passe (initialement 808) on accède à tous les autres paramètres.
Paramètres à accès par mot de passe
Pour entrer dans la liste complète des paramètres, il faut d'abord parcourir la liste de paramètres à accès libre puis entrer le mot de passe dans Loc et continuer à balayer la liste par des appuis bref sur ↻.
Un appui de deux secondes sur la touche ◁ permet de revenir sur le paramètre précédent.
Il y a deux mots de passe : 808 ou la valeur du paramètre PASd. Le choix se fait par le bit de poids 8 (D) du paramètre AF . D=0 pour 808 et D=1 pour valeur de PASd.Il convient donc d'être attentif lors du balayage des paramètres à ne pas modifier intempestivement et inconsciemment, la valeur de AF ou de PASd. Une fois PASd sélectionné dans AF, si vous en avez oublié la valeur vous ne pourrez plus accéder aux paramètres.
Mon paramétrage
Les valeurs des paramètres que j'ai retenues sont portées en rouge dans la colonne la plus à droite de la table des paramètres. Voici quelques explications sur ces choix.
HIAL à AOP : pour le moment je ne me préoccupe pas des alarmes. Les paramètres ont été fixés à des valeurs inatteignables (110 °C, 0 °C). Le reste en découlant pour avoir la paix. Exception LdAL et HdAL alarmes d'écart sont réglées à -0,6°F et autour de 2°F (voir la partie programmation).
Ctrl : pour le moment on choisit la valeur recommandée à savoir APId bien qu'on puisse être tenté par nPID pour éviter la saturation de la correction intégrale sur le premier pas de mise en température initiale de l'empâtage.
Srun : a priori indifférent car j'en modifie la valeur par les touches de panneau de commande
Act : rE ici sans hésitation
At : il s'agit de l'auto-ajustement. oFF pour démarrer. L'auto-ajustement sera déclenché au panneau avant.
P : bande proportionnelle à 5 °C pour démarrer (d'après mon expérience avec le CR20 de Canard Rouge les 23°C d'usine me paraissent forts)
I : action intégrale. Je ne sais pas trop comment démarrer. Je laisse les 200 (valeur d'usine).
d : d'après ce que j'ai lu sur la notice d'autres appareils de ce type, cette valeur est l'une des plus fondamentale pour l'algorithme de contrôle et d'apprentissage. La valeur optimale serait le temps mis pour un four électrique à partir du moment où sa température commence à s'élever pour atteindre une vitesse d'élévation de température de 63,5% de la vitesse d'élévation finale de cette température.
Attention, il ne s'agit pas d'atteindre 63,5% de la température mais de la vitesse d'élévation de la température. On parle de la dérivée de la température.
Je pense que sur un cuve de brassage ce temps est autour de la minute. Je laisse les 50 secondes d'usine
Sur la courbe, il y a un temps de latence, c.-à-d. un temps durant lequel il ne se passe rien. Ce temps est à déduire puisqu'on part du début d'élévation.
Ctl : à ne pas confondre avec Ctrl. Il s'agit de la période de base du contrôle (période de répétition des impulsions de commande sur le SSR). Je parts sur 2 secondes
P2, I2,d2, Ctl2, CHYS : pas concerné. Je laisse à 0.
InP : j'utilise une sonde PT100 donc 21.
dPt : je choisis 0.0 pour la résolution d'affichage.
ScL et ScH : il ne peut rien se passer de fâcheux sur une cuve de brassage (pas de refroidissement et température haute limitée par l'ébullition). Je fixe ces valeurs à -9990 et 32000.
Scb : 0 pour commencer car on ne sait encore rien du système.
FILt : 0 pour commencer. Mes essais on conduit à une valeur de 20.
Fru : 50F on travaille en 50 Hz et degrés Fahrenheit. C'est à vérifier mais il me semble que le filtrage est meilleur dans ce cas. De plus la majorité des recettes sont d'origine anglo-saxonne.
OPt : SSr C'est un SSR que j'utilise
Aut : pas concerné. Je met SSr toutefois.
OPL, OPH, OEF : 0, 100 et 110 on met OEF à 110 °C (valeur inatteignable) pour être toujours limité par OPH. On pourra ainsi une fois l'ébullition atteinte et le programme arrêté, régler OPH pour limiter la puissance de sortie. OPH est placé dans les paramètres de champ.
PAF: 35
- A=1 active la fonction PV préparation
- B=1 mode trempage
- D=1 active la fonction PV démarrage
- F=1 possibilité de commuter suspendu/en marche au panneau avant
Première mise sous tension
La première chose qu'il convient de dire c'est qu'on est nettement plus à l'aise sur un appareil de taille 72x72mm que sur un appareil de taille 48x48mm. L'appui sur les touches est beaucoup plus facile.
Après réparation d'une erreur de soudage dans la prise (erreur orAL clignote sur PV), j'observe que la mesure n'est pas stable avec de l'eau dans la cuve. Dans la notice il est dit que le paramètre FILt permet de filtrer les interférences.
Avec le régulateur CR20 de Canard Rouge je n'avais pas ce problème mais est-ce que ce dernier n'était pas lui-même filtré ? Allez savoir !. Le problème c'est que le filtre introduit un temps de réponse — mais de combien ?
UN PEU DE THÉORIE
Bande proportionnelle
Considérons un système bidirectionnel (chauffage / réfrigération ), en supposant que la correction ne soit que proportionnelle. Celle-ci sera d'autant plus forte (en fonction de l'écart consigne-mesure, ici SV-PV) que la bande proportionnelle P sera étroite. En effet, la bande proportionnelle est définie comme étant la valeur de l'écart qui donne la puissance maximum. La chaleur accumulée lors de la rampe de montée en température va être amortie par cette correction, un peu comme le serait une masse lancée à une certaine vitesse qui s'accrocherait soudain sur un ressort à son élongation maximum. Le ressort attirerait d'abord la masse avec un effort diminuant au fur et à mesure que l'on se rapprocherait de son état de repos, puis ralentirait la masse avec un effort inverse croissant jusqu'à son maximum de compression. On aurait bien sûr des rebonds (oscillations) d'autant plus rapides et forte que le ressort serait raide.
Ici les oscillations sont des oscillations de température et l'amortissement et le risque d'oscillation sont d'autant plus forts que la bande proportionnelle est étroite.
En résumé, plus la bande proportionnelle est étroite, plus la mesure est solidement accrochée à la consigne (sorte de raideur) et plus il y a de risque d'osciller.
Malheureusement une cuve de brassage n'est pas un système bidirectionnel — il n'y a que du chauffage. Cela veut dire que notre analogie a ses limites. L'effet proportionnel inverse n'a d'effet que pour limiter le chauffage demandé par la correction intégrale quand elle existe. Et une fois l'effet total inversé, il ne faut plus compter que sur les pertes thermiques pour voir la température redescendre.
Écart statique
S'il n'y avait pas de pertes de chaleur, une fois la consigne atteinte, la puissance de chauffe retomberait à zéro et les choses seraient stables. Mais dans la situation réelle, l'état stable ne peut être atteint que si la puissance de chauffe compense exactement les pertes. Pour cela il faut donc que la mesure soit inférieure à la consigne. Si on ne peut se satisfaire de cet écart, on verra qu'avec la correction intégrale on peut ajouter une valeur compensatrice et théoriquement rester stable à la valeur de consigne. Mais si cet écart est acceptable, point n'est besoin de correction intégrale car celle-ci engendre d'autres effets négatifs comme le dépassement (overshoot).
Action dérivée
Sans entrer dans les théories mathématiques, disons que la correction dérivée s'entend comme une constante de temps. Plus ce temps est grand plus la correction est forte.
L'action dérivée est là pour amortir les oscillations en s'opposant au mouvement de la mesure. Dans notre analogie du ressort, c'est comme si on plaçait en parallèle du ressort un amortisseur à huile (dash pot). Cet amortisseur va avoir pour effet d'aplatir les rampes.
Action intégrale
L'action intégrale est une action qui s'exprime par un temps qui est d'autant plus faible que la correction est forte. Là encore nous n'allons pas entrer dans les théories mathématiques.
L'action intégrale est obtenue par intégration de l'écart consigne-mesure. Sa valeur est donc proportionnelle à la surface délimitée par la courbe et l'horizontale passant par la consigne. On voit donc que pendant toute la durée de la rampe de montée en température, la correction intégrale va croître par atteindre son maximum lorsque la mesure passera par la valeur de consigne. C'est pourquoi, malgré l'annulation, pus l'inversion, de l'action proportionnelle, on continuera de monter en température et que la valeur de la correction intégrale commencera à diminuer mais beaucoup moins vite car l'écart (maintenant de sens opposé) ne sera pas très important.
On voit donc l'intérêt qu'il peut y avoir à utiliser le mode de commande nPId qui ne commence à intégrer que lorsque l'écart entre dans la bande proportionnelle.
Estimation de la puissance perdue
Pour avoir une idée de la puissance perdue par votre cuve, il faut commencer par connaître sa capacité calorifique.
Eau: 4180 J °C-1 kg-1 (se lit joules par degré Celcius par kilogramme)
Acier 500 J °C-1 kg-1
Grain 1755 J °C-1 kg-1 On peut donc dire que 1kg de grain équivaut à 1755/4180 litres d'eau soit 0,42 litres
Si je me fie au profil du Robobrew il pèse 8,47kg soit l'équivalent de 1/4180*500 litre d'eau 0,12 litres
Pour une recette avec 18 litres d'eau et 5 kg de grain environ l'équivalent de 20 litres d'eau.
Il suffit d'observer la courbe de refroidissement naturel autour de la valeur de consigne.
Prenons un exemple. On a observé une chute de température de 2,11 °C en 10 mn. On a donc perdu 20 kg x 4180 J x2,11 °C soit 176 396 J en 600 secondes. Cela correspond à une puissance de 293 watts.
Si la puissance maximum disponible est 2400 watts et si on tolère un écart statique (correction proportionnelle seule) de 0,3°F, la bande proportionnelle doit faire 0,3 /293 * 2400 =2,46 °F. Cette valeur est la valeur maximum que peut prendre la bande proportionnelle. Une valeur plus basse correspondra à un écart statique plus faible.
Sur mon système, je constate des valeurs de cet ordre de grandeur. Ce qui laisse supposer qu'on pourrait se passer de correction intégrale.
MISE EN PRATIQUE - PARTIE 1 mode nPID
Rappelons d'abord que le mode nPId est un mode dans lequel le régulateur se comporte comme un PID standard, sans intelligence artificielle, et que l'intégration de l'écart n'a lieu que dans la bande proportionnelle.Remarque liminaire : lorsque j'ai réalisé ces essais, je n'avais pas noté que le mode nPId ne disposait pas d'intelligence artificielle. Je conserve cette partie mais la ferai suivre d'une partie 2 en mode APId. Cela permettra d'apprécier les différences. A priori l'avantage est au mode APId. De plus, c'est le mode que conseille fortement le constructeur. Je vous invite donc à ne pas trop fixer votre attention sur cette partie.
Premier auto-ajustement
Pour le moment j'ai opté pour le mode de contrôle nPId. Dans un premier temps j'effectue des auto-apprentissages avec le filtre d'entrée réglé à 8 (le maximum est 40).
Essai fait avec le filtre d'entrée à 8 et les valeurs initiales suivantes : P=100 I=0 d=0 (normalement il les ignore)
Résultats:
P=2,4°F (vous voyez, ma théorie n'est pas si fausse)
I=110
d=27,5
La légende doit s'interpréter comme suit consigne—P/I/d/valeur de Filt P pour pompe en marche , n pour nPID,
La cuve contient 20 litres d'eau, la pompe fonctionne et le couvercle est mis.
Je constate que le filtrage d'entrée n'est pas très bon. J'ajoute donc la courbe verte avec les mêmes réglages mais le filtre réglé à 20.L'augmentation du filtrage rend la lecture des mesures plus facile et ne modifie pas l'allure générale de la courbe.
Deuxième auto-ajustement
Je procède à un nouvel auto-ajustement avec le filtre d'entrée réglé à 20 et les valeurs initiales P=100 I=0 d=0.
Résultats
P=3,9°F
I=148
d=37
Je décide de refaire une série d'essais consécutifs avec des valeurs intermédiaires entre les deux auto-ajustements soit P=2,9°F I=120 d=30.
Il semble qu'il y ait une amélioration d'une courbe à l'autre. Nous sommes hors de la zone de tolérance un court intervalle de temps (entre 4 et 5 minutes) avec des dépassements raisonnables.
Autres essais et réflexions
Pour me faire une idée de l'influences des paramètres j'ai un peu joué avec eux. Je présente quelques exemples ci-après.
Je dois cependant faire remarquer qu'il est un peu difficile d'apprécier l'influence des paramètres car l'appareil semble ne pas se comporter comme un simple PID. On constante que l'intelligence (bonne ou mauvaise ?) bouscule un peu les attentes suite à un changement de paramètre. On a l'impression qu'on vise d'abord un point inférieur à la consigne et cela plusieurs fois de suite. On l'entend au crépitement des bulles d'air sur le fond de la cuve. Il y a plusieurs salves successives. Cela n'est pas mauvais en soi mais rend difficile le réglage des paramètres.
On constate cependant (et cela semble normal) :
- qu'une augmentation de d (dérivée) ralentit la montée en température et cela est surtout visible dans la zone proportionnelle
- qu'une diminution de la bande proportionnelle doit s'accompagner d'une augmentation de la correction dérivée si on ne veut pas trop dépasser.
- qu'une diminution de la correction intégrale (augmentation du paramètre), fait que le dépassement met du temps à se résorber.
Une fois passée la période transitoire, la régulation est stable à +/- 0,1°F.
MISE EN PRATIQUE — PARTIE 2 MODE APId
Auto-ajustement
Nous commençons par un essai d'auto-ajustement avec toujours 20 litres d'eau dans la cuve, pompe en marche, couvercle et filtre d'entrée réglé sur 20.
On remarque que contrairement au mode nPId, les montées en température se font à puissance limitée (la LED OP1 clignote indiquant un rapport cyclique inférieur à 100%).
Les résultats sont :
P=3°F I=152 d=38.
Essais sur échelon de température
On remarque qu'il y a une amélioration entre la courbe bleue et la courbe rouge. Cela pourrait être dû à l'effet d'auto-adaptation annoncé du régulateur.
La courbe 3 (verte et presque parfaite) correspond au cas où la correction intégrale est purement et simplement supprimée. Le résultat confirme ce que j'annonçais dans le paragraphe vaguement théorique plus haut. À savoir, avec des pertes de l'ordre de 300 watts et une bande proportionnelle de 3°F, sachant que la puissance max. (2400 watts) correspond à 3°F d'écart, 300 watts correspondent à un écart statique de 3/2400*300=0,37 °F.
Si nous tolérons 0,6°F d'écart, il n'y a pas lieu d'avoir une correction intégrale qui normalement n'est là que pour ramener la mesure égale à la consigne. Malheureusement, tout le long de la rampe de montée en température, cette correction intégrale croît jusqu'à son maximum lorsque la mesure atteint la consigne. Ce qui explique le dépassement qui traîne à se résorber.
Par ailleurs, il faut signaler que si nous réglons l'alarme d'écart bas à -0,6°F le compteur de temps des pas de programme, qui se déclenche lorsque l'alarme d'écart bas disparaît, c.-à-d. lorsque nous entrons dans la bande de tolérance (en vert pâle sur la figure), se déclenchera au moment le plus opportun.
PROGRAMMATION
Pour saisir un programme, il faut d'abord avoir accès aux pas de programme. Pour cela nous accédons au paramètre Pno (normalement en tête de liste des paramètres à accès libre si vous avez suivi mes conseils) et lui donnons une valeur au moins égale au nombre de pas auxquels nous voulons accéder.
En effet, non seulement Pno indique la valeur du pas en cours mais donne aussi accès aux pas pour programmation.
Pour accéder aux pas de programme, dans le mode d'affichage normal, il faut un appui de 2 secondes sur la touche ◁.
On se reportera à la notice pour plus d'explication. Voici un exemple de programme (température en degré Fahrenheit et temps en minutes).
L'exemple suppose que :
- le mode Trempage (soak) est activé (bit B du paramètre PAF à 1)
- la fonction préparation (rdy) est activée ( Bit A du paramètre PAF à 1 — contrairement à ce que dit la documentation en anglais à cette date).
- les valeurs LdAL et HdAl (alarmes d'écart) sont réglées à -0,6°F pour LdAL et à environ 2°F pour HdAL.
Exemple PAF=35
N° du pas | SP (consigne) | Temps | Explication |
---|---|---|---|
1 | 153 | 2 | Ici on cherche à atteindre la "strike temperature" (fournie par de nombreux calculateurs en fonction du volume d'eau de mash et du poids du grain) |
2 | 153 | 0.0 | 0.0 est un code indiquant un état suspendu. Le régulateur régule sur 153 °F et le temps importe peu. Ici cela laisse le temps à l'opérateur une fois la température atteinte de passer au pas suivant (appui sur la touche ▽ run) et de tout de suite mettre le grain dans la cuve. |
3 | 151 | 60 | Le premier palier d'empâtage. Il va durer 60 minutes à la température de 151 °F. |
4 | 169 | 10 | Un palier de 10 minutes pour le mash out. |
5 | 230 | 0.0 | Passe en mode suspendu. L'opérateur peut attendre l'ébullition et appuyer sur la touche ▽ (run) une fois le hot break passé. |
6 | 212 | 90 | Le comptage du temps d'ébullition démarre car les 212 °F sont déjà atteints. Une fois dans ce pas l'opérateur remonte la consigne et règle OPH (limitation de puissance) |
7 | 32 | -121.0 | Arrêt |
Note1 : le pas 1 peu apparaître comme superflu. Néanmoins, si on lance le programme par appui sur la touche ▽ (run), cet appui dure assez longtemps pour être interprété comme commande de sortie de l'état suspendu. Cela ferait sortir du pas 1 (devenu 2) immédiatement, avant même d'avoir atteint la cible de 153 °F.
Note 2 : au pas 3, si la "strike temperature" est mal calculée. On risque d'entrer dans ce pas en dehors de la plage de tolérance [SV+LdAL, SV+HdAL] qui enclenche le comptage.
Dans un tel cas, on devra attendre que la température revienne dans cette plage pour que le comptage de temps démarre. Mais de tout façon, ce serait la même chose sans programmation.
Par ailleurs, il vaut mieux provoquer le passage au pas suivant juste avant d'introduire le grain. Dans le cas inverse, la régulation resterait calée sur la "strike temperature" et le système se mettrait à chauffer pour atteindre cette cible. Alors qu'en le faisant avant d'introduire le grain, la cible deviendrait la température du premier pas d'empâtage ce qui est ce que nous recherchons.
Note 3 : au pas 6 on devrait donner la température d'ébullition exacte. Si l'ébullition a lieu à une valeur différente. Il faut absolument qu'elle se trouve dans la plage [SP+LdAL ,SP+HdAL]. (LdAL est négatif). C'est dans cette plage que se déclenche le compteur de temps du pas. Attention si vous êtes en altitude. Dans le doute prenez une casserole et un thermomètre et vérifiez. Pour assurer le coup, on peut donner une valeur légèrement inférieure à la température réelle d'ébullition, et élargir le HdAL. De toute manière, dans le pas précédent, l'opérateur attend que l'ébullition réelle ait bien lieu ("hot break").
CONCLUSION
Ce régulateur semble correspondre à mes attentes. Il faut un peu de temps pour se familiariser avec son mode de paramétrage mais une fois les choses comprises il est assez facile à utiliser dans le cadre du brassage.
Je n'ai pas encore eu l'occasion de l'utiliser en brassage réel mais je n'attends pas, a priori, de surprise. J'ai d'ailleurs fait une simulation avec 18 litres d'eau et en ajoutant l'équivalent de 5 kg de grain soit 2,1 litre d'eau en calculant le température d'attaque. Tout s'est passé comme prévu. Les paliers ont été rapidement atteints et la régulation très satisfaisante.
Je pense utiliser le mode APId sans correction intégrale qui semble offrir une réponse rapide et précise.
INVENTAIRE DES MATÉRIELS ACHETÉS
Matériel | Marque | Prix en € | Port en € | Total | Lieu d'achat |
---|---|---|---|---|---|
Régulateur AI 518P program SSr | Xiqi E&Tech | 59,5 | 0 | 59,5 | AliExpress |
Boîtier alu 155x120x83 mm | Advanced Tools Store | 14,45 | 0 | 14,45 | AliExpress |
Prises aviation | Locheuk RF Series Store | 4,6 | 6 | 10,6 | AliExpress |
Relais SSR CDG1 - 1DA/40A | Delixi | 9,5 | 4,6 | 14,1 | AliExpress ou
microbrassage.com |
Nota : les matériels venus de Chine ont tous été livrés dans les 15 jours.